10 essential tips to enhance efficiency in your plastic manufacturing business
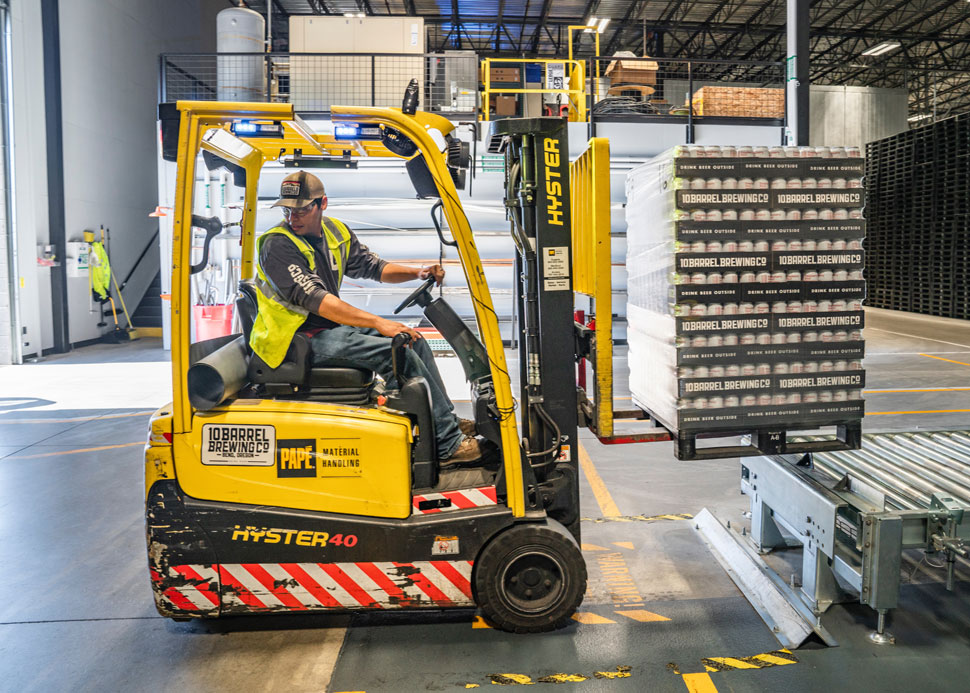
Efficiency is key to maintaining profitability and staying ahead in the highly competitive plastic manufacturing industry. With increasing global competition and rising costs, businesses must proactively optimize their operations.
Let’s look into 10 crucial strategies plastic manufacturing businesses can deploy to enhance operational efficiency. From implementing lean manufacturing principles to leveraging digital tools for business management and accounting, these actionable tips aim to equip managers and decision-makers with ways to maximize productivity, reduce waste, and ultimately boost their bottom line.
Implement Lean Manufacturing Principles
Plastic manufacturing businesses should consider implementing lean manufacturing principles as a first step toward optimizing efficiency. Lean manufacturing is a comprehensive strategy that aims to eliminate waste and streamline processes, resulting in reduced costs, improved product quality, and shorter turnaround times. This approach focuses on increasing value-added work that enhances the service or product, delivering more value to the customers.
Lean principles can significantly impact the plastic manufacturing industry. For example, the “Just-in-time” (JIT) approach, a key part of lean manufacturing, ensures that raw materials and components are only ordered and produced when there is demand, minimizing waste and reducing inventory costs.
Another major aspect of lean manufacturing is the focus on continuous improvement, also known as Kaizen. In a plastic manufacturing context, this could mean persistently working on improving processes, machinery efficiency, and staff skills, all of which are critical components for boosting overall productivity.
Implementing lean manufacturing is not an overnight process, but with commitment and focus, it can significantly enhance productivity and profitability. Expert guidance in implementing such principles can ensure the process is done correctly and yields the expected results.
Use Hot Runner Technology for Injection Molding
Efficient hot runner systems in plastic manufacturing represent a significant leap forward in injection molding technology. Compared to traditional cold runner systems, hot runner technology can offer faster cycle times, reduced waste, and improved part quality—all critical aspects in a manufacturing environment that prizes efficiency and cost-effectiveness.
Hot runner systems work by maintaining a molten state of the plastic within the runners of the mold. This removes the need for regrounding and recycling of plastic, thereby minimizing the production of waste material. Additionally, hot runner systems can produce more consistent parts, reduce labor needs, and increase production speed. Despite the higher up-front cost, the return on investment over time is substantial due to lower material usage, improved quality control, and less manpower.
Optimise Your Supply Chain
There must be a more profound focus on supply chain optimization to enhance operational efficiency in a plastic manufacturing business. The supply chain, involving everything from sourcing raw materials to delivering finished products, plays a pivotal role in the overall efficiency and profitability of the manufacturing process.
The first step is to ensure that you have reliable suppliers that deliver high-quality materials promptly. Constant delays or issues with raw material quality can significantly disrupt your manufacturing process, resulting in lost time and money. Maintaining a good relationship with suppliers can also yield benefits like cost reductions or priority during peak times.
On the delivery side, finding cost-effective, efficient methods to get your products to customers is equally important. Whether it’s finding the best shipping partners or maintaining a strategic distribution network, efficient delivery channels help ensure customer satisfaction and the company’s profitability. Implementing advanced supply chain analytics and management software can provide insights into potential inefficiencies and suggest areas for improvement.
Invest in High-Quality Equipment and Maintenance
Investing in high-quality, modern machinery can drive efficiency in a plastic manufacturing business. Advanced machines can offer higher productivity rates, superior precision, lower energy consumption, and improved user safety. Although the up-front cost can be high, the long-term benefits in terms of efficiency, reduced downtime, and product quality make it worthwhile.
But purchasing high-quality equipment is just half of the equation. Regular maintenance of these devices is equally important. Planned, proactive maintenance not only helps avoid sudden malfunctions, leading to production delays and potential losses but also extends the lifespan of your equipment. Therefore, implement a robust maintenance schedule that includes regular inspections, cleaning, and preemptive replacements of worn-out parts.
Train Staff on Efficient Operation and Quality Control
A workforce well-trained in operating machines efficiently and controlling the quality of output can significantly contribute to the efficiency of a plastic manufacturing business. Staff training should be viewed not as an expense but as an investment toward better productivity.
Ensure your staff members are comprehensively trained in operating your machinery and equipment. This minimizes the potential for errors, leading to lower defect rates, and helps prevent costly machine breakdowns due to improper usage.
In addition, training employees in quality control measures helps maintain consistency in product quality, enhancing customer satisfaction and reducing the costs associated with defective items. Remember, a well-trained employee is more productive and can identify potential problems and suggest improvements, paving the way for continuous enhancements to your business processes.
Improve Warehouse and Inventory Management
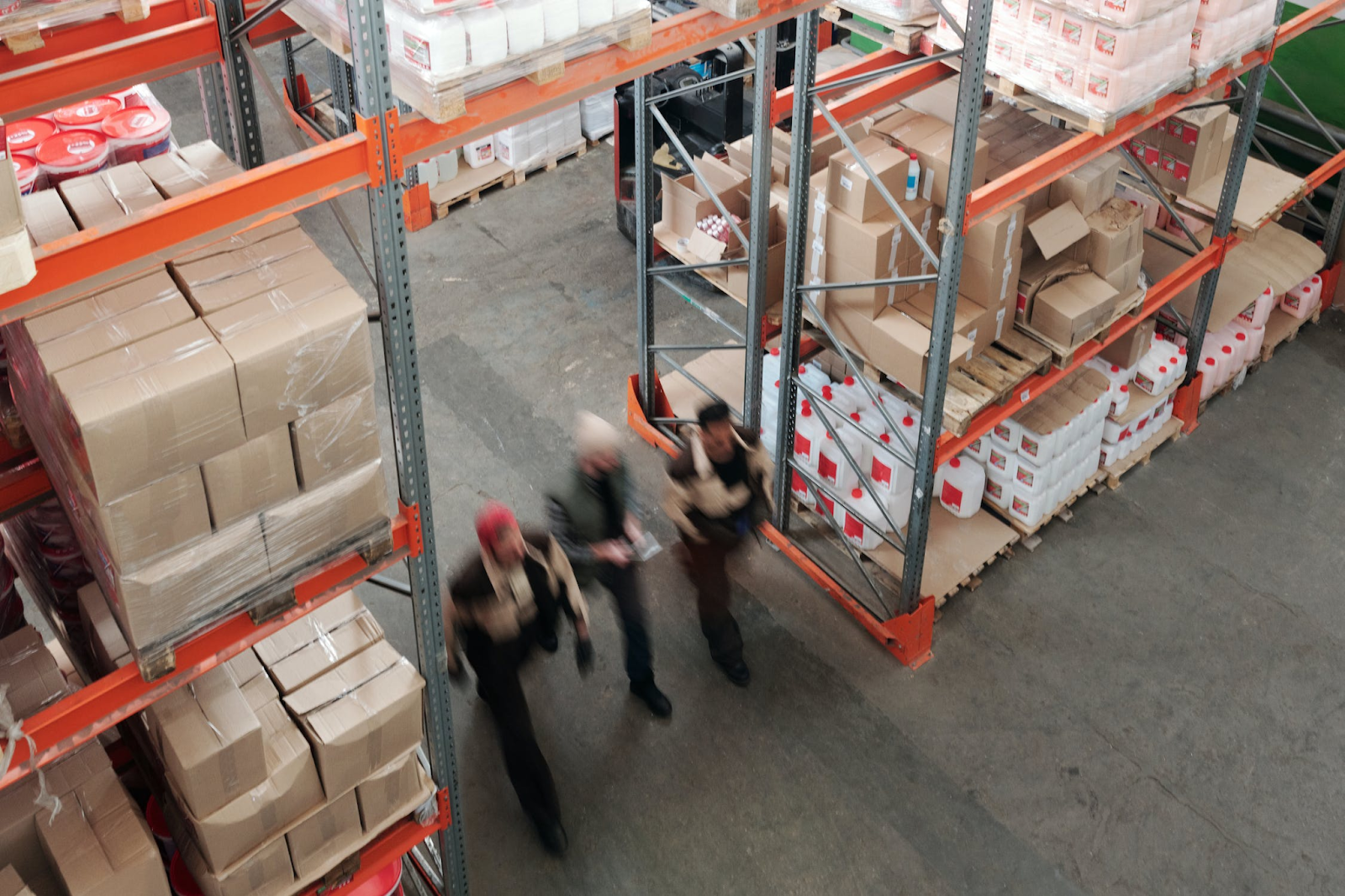
Efficient warehouse and inventory management directly contribute to the smooth functioning of plastic manufacturing businesses. Implement a management system that provides real-time inventory levels, tracks the movement of goods within the warehouse, and quickly responds to changes in demand.
Synchronization of production with inventory levels is crucial to prevent overproduction or stockouts. It’s critical to use techniques like real-time tracking, demand forecasting, and automated reordering to ensure optimum inventory levels at all times. A well-organized warehouse that allows easy access and quick retrieval of goods significantly reduces time wastage.
Adopt Energy-Efficient Practices
Creating an energy-efficient environment in a plastic manufacturing business can greatly reduce operational costs and improve overall efficiency. Consider investing in energy-saving machinery, retrofitting older equipment with energy-efficient parts, and promoting energy-conserving practices among your workforce.
Installing energy-efficient lighting systems and improving insulation can significantly reduce energy usage. Regular energy audits can also help identify areas of excessive energy consumption and provide insights into possible solutions.
Given the energy-intensive nature of plastic manufacturing processes, small improvements in energy efficiency can lead to considerable cost savings in the long run. Additionally, it reflects well on the company’s commitment to environmental responsibility, enhancing its image among customers and stakeholders.
Streamline Production Processes
Carefully examining and refining your production processes can significantly improve efficiency. Take time to review each phase of your operation, identify bottlenecks or inefficiencies, and implement necessary strategies to streamline them.
This might involve redesigning the workspace layout for better workflow, adopting newer production techniques, establishing clear protocols to minimize errors, or investing in automated systems to reduce manual labor.
It’s crucial to involve employees in this process as they offer a front-line perspective on where improvements can be made. A streamlined manufacturing process speeds up production time, lowers costs, and improves product quality.
Implement a Continuous Improvement Strategy
A culture of continuous improvement can drive efficiency in a plastic manufacturing business in the long term. Based on the Kaizen philosophy of continuous, incremental improvements, this strategy encourages every organization member to look for ways to improve their work processes regularly.
It’s crucial to encourage employee feedback and ideas, regularly review and update processes, and maintain an open mind to innovative practices. This approach ensures your operations continue evolving, always aiming for efficiency, better quality, and cost reductions. It can foster a proactive atmosphere where each team member feels involved and responsible for the business’s success. To make this process structured, consider using systematic approaches like Six Sigma or Total Quality Management.
Use Digital Tools for Business Management and Accounting
Leveraging digital tools for business management, including tasks like inventory control, project management, and accounting, can bring about a profound increase in efficiency for your plastic manufacturing business. Technology has the potential to automate routine tasks, provide crucial metrics for performance analysis, and streamline many administrative processes that can otherwise be time-consuming.
For example, adopting accounting software simplifies financial tracking, aids in budgeting, and ensures regulatory compliance. Alternatively, outsourcing accounting tasks to experts in the field and these tools can also be a strategic move for businesses. It saves time and resources to be better utilized for core business activities and provides access to professional expertise and advanced resources. This approach guarantees accurate financial management and timely statutory submissions and ultimately supports informed decision-making for strategic business growth.
Similarly, project management tools help keep track of deadlines, delegate tasks, and ensure smooth communication across teams. Customer relationship management (CRM) software can also improve sales efforts and customer service.
Automating these tasks can free up valuable time that can be better spent on strategy and decision-making processes, enhancing the overall productivity of your business. Given the wide array of digital tools available today, it’s important to choose ones that best match your specific needs and integrate seamlessly into your existing operations.
The Bottom Line
Optimizing the efficiency of a plastic manufacturing business is a multifaceted task involving various elements: from leveraging advanced technologies and streamlining the supply chain to personnel training and implementing continuous improvement strategies.
While adopting these strategies may require initial investment and effort, the potential benefits in terms of cost savings, improved product quality, enhanced customer satisfaction, and sustainable growth make it well worth it.
As we move into an increasingly competitive market space, the focus on operational efficiency will continue to intensify. Businesses that commit to efficiency optimization stand to gain a strong competitive edge and pave the way for long-term success in the manufacturing industry.